FROM: MARIO TORTORA /JUAN DIEGO UMANA
SUBJECT: BUILDING MAINTENANCE
SAFETY RULES:
1. The power of electricity can be dangerous if it's not used correctly. Electrical energy can
damage property and ignite fires. It can also hurt and even kill.
2. Safety practices can help minimize electrical hazards and cut down the risk of accidents. The hazard of electricity cannot be eliminated, but it can be controlled though education and engineering. The more you understand about electrical energy the safer you'll be at work and home.
3. You can get an electric shock if you touch a grounded surface and hazardous electrical equipment at the same time. The shock happens when the flow of electric current (amperage) from the electrical equipment goes through your body to the ground. How serious the injury depends on what part of your body receives the current. It also depends on how long the electric current flows. Just a small am
ount of amperage can hurt or be fatal.
4. Closing electrical control panels and covering receptacle boxes.
5. Avoid working in and around wet or damp conditions, equipment and electrical currents that aren't grounded, and wires that aren't insulated
6. Avoid touching water, damp surfaces, ungrounded metal and bare wires if you're not protected
7. Safety Maintenance Person diligent crew assures that all holes greater than 2" are safely covered and properly marked. Various hole covers are available.
8. 3/4" plywood hole covers can be fastened down to the deck, or the hole cover can be created for easy removal while maintaining its position over the hole. Metal plate hole covers are strong, durable and clearly marked. All hole covers are maintained by Safety Guys and recycled to the upper floors to maximize cost efficiencies.SUBJECT: BUILDING MAINTENANCE
SAFETY RULES:
1. The power of electricity can be dangerous if it's not used correctly. Electrical energy can
2. Safety practices can help minimize electrical hazards and cut down the risk of accidents. The hazard of electricity cannot be eliminated, but it can be controlled though education and engineering. The more you understand about electrical energy the safer you'll be at work and home.
3. You can get an electric shock if you touch a grounded surface and hazardous electrical equipment at the same time. The shock happens when the flow of electric current (amperage) from the electrical equipment goes through your body to the ground. How serious the injury depends on what part of your body receives the current. It also depends on how long the electric current flows. Just a small am

4. Closing electrical control panels and covering receptacle boxes.
5. Avoid working in and around wet or damp conditions, equipment and electrical currents that aren't grounded, and wires that aren't insulated
6. Avoid touching water, damp surfaces, ungrounded metal and bare wires if you're not protected
7. Safety Maintenance Person diligent crew assures that all holes greater than 2" are safely covered and properly marked. Various hole covers are available.
9. Keep motors, cords, appliances dry and away from water at all times.
10. Use equipment and tools the way they are designed to be used.
11. Report immediately any damage or defective equipment, power hand tools or machinery.
12. Don't wear metal jewelry that might make contact with electric current.
13. Wear eye protection where required.
14. Wear rubber-soled shoes or boots on damp or wet surfaces.
15. Wear safety-approved rubber and leather gloves when you work with electricity
16. Check the surrounding area for spills, dampness or water.
17. Check connections and ground wires to be tight and free from breaks.
18. Check circuits and wiring are in good repair and not overloaded.
19. Check insulation for worn spots or breaks that could cause a shock.
20. Check the condition of cords and extension cords.
21. Check and maintain equipment to make sure it's working right and free of defects or damage. 22. Check equipment belts and gears to detect excess tension or binding that can cause a power overload.
23. Check that personal protective hand and foot protectors are kept in good repair and readily available.
24. Immediately report any hazards, damage and defective equipment, tools and machinery to a supervisor or manager.
25. Know where are located all Switch off power at the fuse or circuit-breaker box, for any machines.
26. Don’t tie or knot cords. Don’t let furniture sit on cords.
27. The electrical outlet in the bathrooms and outside, should have a Ground Fault Circuit Interrupter (GFCI.) This is a tool that protects you from a dangerous shock when water and electricity come together. An electrician can install a GFCI for you.
28. All electrical outlets and switches in the building should be covered by “faceplates”.
29. All electrical cords should be in good condition.

POSITION DESCRIPTION:
1. Skills and knowledge in: Carpentry, Electrical, Plumbing, HVAC, Mechanical, Painting, Welding, Network, Structured wiring, informatics area, CT and Remote access. Must be able to learn new skills, be able to teach skills already obtained. Report all problems and solutions.
2. Creates checklists of maintenance routines (location of gauges, proper gauge readings, etc. preventive maintenance routines and guidelines
3. Purchases Orders supplies with approval of Board members. Distributes maintenance supplies to Maintenance employees sufficient for their daily needs.
4. Maintains and controls maintenance inventory on computers files.
5. Receives and signs for maintenance supply deliveries.
6. Supervises safe workplace practices. The safety it’s our Goals.
7. The Maintenance Engineer is one of the most important jobs in the building. The uninterrupted operation of the condominium rest on his or her expertise to solve difficult problems that must be encounter in the day to day operation of the facilities. The time and knowledge is the most important item in an emergency.
8. Report at Samantha Williams once a month the most important labors for the News letter.
9. Complete report at the Board meeting the maintenance report.
10. Must provide leadership and knowledge in supervising the staff.
11. Supervising, maintenance and repair:
A. IRRIGATION SPRINKLERS
B. Motors Working, updated and maintenance.
C. Valves, Timers, drives, photocell in right Working.
D. Minor Repairs in Trash chute, elevators, gates and all items under other contractors companies.
E. DRAIN CLEANING.
F. Maintenance and repair pump at the Septic tank.
12. Supervise all outside contractors.
13. Inspect sound proof in the new floor inside the apartment.
14. During working hours, the maintenance supervisor must inform for any trip outside of the building and the reason for it.
Train all personnel for emergency situations, such as, sprinkler systems, fire emergency, generator, water valves, garage door system, etc.
Groom the assistant maintenance supervisor in all areas of the maintenance job, in order for the assistant to take over in case of emergency.
Must be on call 24 hours through a beeper provided by the association.
Emergencies must be answer promptly through instructions of the personnel on duty or by direct intervention and always notify the manager.
18. Will have access to individual units upon request in case of an emergency and with the approval of the Board.
19. Check roof pumps.
20. Maintenance Main A/C, Cooling Tower, Air Handles, Domestic Pump Water and Main Electrical Rooms.
21. Start up diesel Motor one time at the week (Preferred Saturdays).
Motor/Generator Inspection.
23. Communicate information regarding future maintenance needs.
24. Inspect wiring and electrical control for lose connections; charring, broken or wet insulation to prevent short circuits.
25. Operate motors/generator to check for excessive heat and vibration.
26. Updated and find all catalogues for our equipments.
27. Programming, reviewing and changing the irrigation sprinkler timer, according with city regulations and/or own requirements.
28. Programming, reviewing and changing the lighting timers and photocells, according with our own requirements.
29. Inspect any permanent or transitory electrical connection should be made in accordance with the requirements of the National Electrical Code and other state and local codes.
30. Inspect sound proof accord Board Regulation in new floor (Tile, wood, marble) installed.
31. Identify types and classes of personal protective equipment (PPE).
32. Reduce Hazards of Electricity, Mechanical and other workers risk.
33. Bring Personal Protective Equipment.
34. Look for the Underwriters Laboratories (UL) mark on the label when you buy electrical appliances (such as motors, drives and all equipment) and cords.
35. Inspected the equipment, tools, machines and lights to make sure they operate according to electrical code requirements.
36. Extensions cords, motors, equipment and appliance cords in good repair and are properly rated for the way they're intended to be used.
37. Protecting circuits with Ground Fault Circuit Interrupters (GFCI).
38. Looking for posted signs that identify electrical hazards, or other risk.
MAINTENANCE TECH:
Must show a wide knowledge of plumbing, electricity, carpentry, masonry, welding, etc. to be able to do the work and deal with the outside contractors and inspectors.
THE FOLLOWING ITEMS MUST BE CHECKED:
Inspect the main air conditioning on the roof. Also check the roof for sign of deterioration and debris Notify promptly the manager for any damage.
Inspect the generator and water pump.
Review before and after any work of maintenance is performed in the air conditioning equipment, on the roof. Make sure that tools are removed and the area is clean after leaving the job.
Maintain inventory of equipment and maintenance supplies.
Will have access to individual units upon request in case of an emergency and with the approval of the manager of the building.
Check oil level in gear boxes located on the cooling towers
Check all motors and belts.
Check vents on hallways.
Exit doors must close and catch.
Trash chutes: Small and fast repair (Reset the compactor and Electrical Boxes).
Elevator lights and floor level.
Change all batteries in smoke alarms throughout the building as needed.
Check to find if a renovation is taking place on any floor.
Change filters in every each A/C Units and Air Handle Units.
Check lobby and social room lighting fixtures.
Check all lighting, indoor and outdoor.
Storage room lighting and Safety.
Maintenance electricity and Sprinkler system in Front entrance.
Knowledge about Sewer station and drain.
Maintenance and Repair Pump and Generator Room.
Maintenance A/C Motor and belt.
Maintenance A/C in first, second and seventh floor.
Check mounting bolts, guards and brackets as applicable.
Lubricate motor and generator as required. Do not over lubricate.
Inspect for rust and corrosion. Remove rust and corrosion and apply paint where required.
Check the temperature of the spa and the pool. The spa temperature should be between 98 and 103 degrees Fahrenheit. The maximum safe temperature for the spa is 104 degrees Fahrenheit.
Check pool temperature twice a day, to maintain a comfortable temperature between 78-82 degrees Fahrenheit.
Check the roof area. Walk the entire area and report anything unusual.
Check for proper operation conditions of all air conditioner, hallways, lobby, exercise room, social room, etc. Report, anything out of the ordinary function.
Walk both stairwells and check for burned out lights, door jams, weather stripping that need to be replaced or anything to be done by you or any other employee.
Check all emergency and Exit signals light.
Walk the garage and check all lights and replace as needed. Check the parking spaces for any residue of oil or transmission fluid and report to the management right away.
Pour disinfectant down garbage chutes to sanitize, clean or maintenance.
Every Friday turn on all the outside common area lights and replace as needed.
Report for further assignment, after completing the daily rout.
Change wall socket and other electrical components accord electrical code
Check hallway a/c units.
Paint all Equipments, Pipes, Fire Sprinkler pipes, motors and Wall when it’s needed.
Preserve, tune up, upgrade and Maintenance machineries and equipment.
AC/DC fundamentals, Ohm’s Law, typical load and generation concepts.
Relationships between voltage, ohms, amperes, three-phase voltage, current and power AC/DC circuits.
Use the right light bulbs in all lamps and light fixtures.
NORMAS PARA UNA LARGA VIDA DE SU A/C
1. Su unidad de A/C consta de dos partes:
a. Air handler que se encuentra dentro del closet(cercano a la puerta de su apartamento).

b. Condenser unit: Que se encuentra en el Roof del Edificio. Nustras unidades de A/C requieren de agua para operar, es pore eso que cuando se va a dar Mantenimiento a las Torres de Frio o a los Raiser se ordena apagar los A/C de los Apartamentos.
2. Opere su termostato entre 75 y 78 Grados.
3. Usted debe cambiar los filtros cada 30 dias, ya que el polvo entrara a su maquina o a su apartamento.
4. No almacene pinturas, disloventes, liquidos de limpieza u otros materials que puedan afectar su salud, ya que los vapores los respira usted y pueden causar deterioro de su salud.
5. Si el equipo no opera normalmente, apague el A/C de los Breakers que se encuentran dentro del apartamento en la Caja Electrica, deje pasar un par de minutes antes de operarla. Los primeros minutos verifique que no hayan ruidos u olores a quemado. Revise qu

6. Se recomienda hacerle un Mantenimiento a su A/C semestral o maximo anual por una empresa de Aires Calificada.
7. Si usted require llamar un tecnico para reparar su maquina, este seguro de que la Compania que usted llama tiene Licencia y Seguros contra la Propiedad, contra danos en su equipo o contra accidents del mismo operario. Esto es requerido por ley para prevenir danos a su Equipo o al Edificio.
8. Mantenga una llave de repuesto en la Caja de Llaves del Frontdesk, podrian necesitarla e su ausencia.
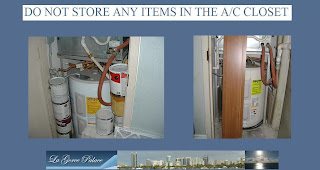
9. Los A/C funcionan con 220 Voltios, no trate de maniobrar dentro de las unidades sin suficiente proteccion y conocimiento, puede causar descargas electricas o la muerte.
COOLING TOWERS
CLOSED CIRCUIT COOLING TOWERS
Maintenance Check List
EVAPORATIVE CONDENSERS
Type of Service: Once a Month.
1. Check fan bearings and lubricate,
if necessary.
2. Check tightness and adjustment of
thrust collars on sleeve bearing units
and locking collars on ball bearing units.
3. Check belt tension and adjust
if necessary. For gear drive units, check
oil level.
4. Clean strainer (if atmosphere is
extremely dirty, it may be necessary to
clean strainer weekly).
5. Check for biological growth in basin.
Consult water treatment specialist if
such growth is not under control.
6. Clean and flush basin.
7. Check spray distribution system. Check
spray branches and clean as necessary.
Check and re-position nozzles, if necessary.
8. Check operating water level in the basin
and adjust float valve, if required.
9. Check bleed rate and adjust
if necessary.
10. Check fans and air inlet screens
and remove any dirt or debris.
COOLING TOWERS
CLOSED CIRCUIT COOLING TOWERS
Maintenance Check List
EVAPORATIVE CONDENSERS
Type of Service: Once a Month.
1. Check fan bearings and lubricate,
if necessary.
2. Check tightness and adjustment of
thrust collars on sleeve bearing units
and locking collars on ball bearing units.
3. Check belt tension and adjust
if necessary. For gear drive units, check
oil level.

4. Clean strainer (if atmosphere is
extremely dirty, it may be necessary to
clean strainer weekly).
5. Check for biological growth in basin.
Consult water treatment specialist if
such growth is not under control.
6. Clean and flush basin.
7. Check spray distribution system. Check
spray branches and clean as necessary.
Check and re-position nozzles, if necessary.
8. Check operating water level in the basin
and adjust float valve, if required.
9. Check bleed rate and adjust
if necessary.
10. Check fans and air inlet screens
and remove any dirt or debris.
Once a Year: Inspect and clean protective finish inside and out. Look particularly for any signs of spot corrosion. Clean and refinish any damaged protective coating.

Before undertaking start-up procedures or performing inspection or maintenance of BAC equipment, make certain the power has
been disconnected. Refer to appropriate operating and maintenance manuals and comply with all caution label instructions.
Suggestions for Spring Start-Up of
Your Evaporative Cooling Equipment
1. Inspect the Unit.
a. Check position of strainer screens and air inlet screens to be
sure screens have not shifted during shutdown.
b. Check fans, bearings, fan motors, and pumps (if applicable) for
lubrication. See item 5.
c. Rotate all fan shafts by hand to make sure they turn freely.

Before undertaking start-up procedures or performing inspection or maintenance of BAC equipment, make certain the power has
been disconnected. Refer to appropriate operating and maintenance manuals and comply with all caution label instructions.
Suggestions for Spring Start-Up of
Your Evaporative Cooling Equipment
1. Inspect the Unit.
a. Check position of strainer screens and air inlet screens to be
sure screens have not shifted during shutdown.
b. Check fans, bearings, fan motors, and pumps (if applicable) for
lubrication. See item 5.
c. Rotate all fan shafts by hand to make sure they turn freely.
d. Check fan motor
s for proper rotation. Directional arrows on fan
cowls or housings indicate correct rotation.
e. Clear fans of any trash or debris that may have accumulated
during shutdown.
f. Check make-up valve for shut-off ability. Check float ball for buoyancy.
g. Check spray nozzles for proper distribution.
h. Check surface for scale, sludge or debris and clean if necessary.
i. Check access door gaskets and replace, if necessary.
j. Check the condition of the cooling tower fill. If it is clogged or
deteriorated, replace it with Factory Authorized Replacement Fill.
2. Inspection of Casing.
a. While the unit is still drained, thoroughly inspect the unit casing.
Clean and touch-up any areas showing signs of deterioration.
For galvanized steel construction units, any damaged area
should be cleaned to bare metal and refinished with Zinc-Rich
Compound (ZRC). This is also the time when any casing joint
leaks can be easily repaired.
b. Remove any deposits that have built up and were not cleared by
flushing the basin. Touch up the area beneath deposits as required.
3. Fill the Cold Water Basin withFresh Water to the Overflow level.
a. At initial start-up or before restart-up where the basin was
completely drained; the initial biocide treatment should be
applied at this time (see Water Treatment section of the
appropriate maintenance manual).
b.
Following a shut-down period, where the basin was not
completely drained: It is recommended that an initial shock
treatment of appropriate biocides be administered at restart-up
to eliminate accumulated biological contaminants.
4. Fill Basin with Water and Check Float
Valve Level.
After the unit has been in operation under load for several days,
operating water level should be checked. Check the Operating and
Maintenance Manual to determine the proper operating water level.
5. Adjust Belt Tension of Fan Motors.
Proper belt tension is determined by pressing against a single belt
midway between sheaves with one finger, which should deflect the
belt 1/2” with moderate pressure. To adjust belts, loosen locknut on
the motor base and rotate the exterior nut as necessary. Re-tighten
locknut and recheck tension.
6. Lubricate Bearings.
a. Sleeve Bearings: Use the BAC oil that was shipped with the unit.
During the first week of operation, refill each bearing cup several
times to saturate the felt wick in the bearing cartridge. DO NOT
USE OILS CONTAINING DETERGENTS FOR LUBRICATION.
b. Ball Bearings: Purge bearings with new grease.
c. Fan Motors/Pumps (If applicable): Lubrication should be in
accordance with motor manufacturer’s recommendations.
Suggestions for Winterizing
Evaporative Cooling Equipment:

cowls or housings indicate correct rotation.
e. Clear fans of any trash or debris that may have accumulated
during shutdown.
f. Check make-up valve for shut-off ability. Check float ball for buoyancy.
g. Check spray nozzles for proper distribution.
h. Check surface for scale, sludge or debris and clean if necessary.
i. Check access door gaskets and replace, if necessary.
j. Check the condition of the cooling tower fill. If it is clogged or
deteriorated, replace it with Factory Authorized Replacement Fill.
2. Inspection of Casing.
a. While the unit is still drained, thoroughly inspect the unit casing.
Clean and touch-up any areas showing signs of deterioration.
For galvanized steel construction units, any damaged area
should be cleaned to bare metal and refinished with Zinc-Rich

Compound (ZRC). This is also the time when any casing joint
leaks can be easily repaired.
b. Remove any deposits that have built up and were not cleared by
flushing the basin. Touch up the area beneath deposits as required.
3. Fill the Cold Water Basin withFresh Water to the Overflow level.
a. At initial start-up or before restart-up where the basin was
completely drained; the initial biocide treatment should be
applied at this time (see Water Treatment section of the
appropriate maintenance manual).
b.

completely drained: It is recommended that an initial shock
treatment of appropriate biocides be administered at restart-up
to eliminate accumulated biological contaminants.
4. Fill Basin with Water and Check Float
Valve Level.
After the unit has been in operation under load for several days,
operating water level should be checked. Check the Operating and
Maintenance Manual to determine the proper operating water level.
5. Adjust Belt Tension of Fan Motors.
Proper belt tension is determined by pressing against a single belt
midway between sheaves with one finger, which should deflect the
belt 1/2” with moderate pressure. To adjust belts, loosen locknut on
the motor base and rotate the exterior nut as necessary. Re-tighten
locknut and recheck tension.
6. Lubricate Bearings.
a. Sleeve Bearings: Use the BAC oil that was shipped with the unit.
During the first week of operation, refill each bearing cup several
times to saturate the felt wick in the bearing cartridge. DO NOT
USE OILS CONTAINING DETERGENTS FOR LUBRICATION.
b. Ball Bearings: Purge bearings with new grease.
c. Fan Motors/Pumps (If applicable): Lubrication should be in
accordance with motor manufacturer’s recommendations.
Suggestions for Winterizing
Evaporative Cooling Equipment:
1. Provision must be made to protect the water in the basin fromfreezing when the unit is idle. This can be accomplished by using
a remote sump installed in a heated space or installing steam/hot
water coils or electric immersion heaters in the
tower basin.
2.All outdoor water lines, including the make-up water line to theunit and drain lines from the unit should be traced with heater
cable and insulated.
3. During operation, frequent visual inspections of the unit mustbe performed regularly to:
a. Insure all operating controls are properly set and functioning
normally.
b. Insure the method of freeze prevention is effective.
c. Discover any icing conditions before they develop to the point
where the unit is damaged or system performance is impaired.
4. A regular preventive maintenance program must be established
and carried out despite adverse weather conditions. Items
covered should include:
a. Regular lubrication of moving parts.
b. Regular checking of the make-up value and cleaning of
strainers to prevent high water levels in basin.
c. Regular checking and cleaning of hot water distribution system
to assure uniform flow over unit.
Coil Protection for Closed Circuit
Cooling Towers
1. Charge the coil with ethylene glycol to prevent the system fluid from freezing. The percentage of ethylene glycol should be determined based upon the conditions in your area.
2. If no ethylene glycol is used, adequate* flow through the coil must be maintained so that the temperature of the circulating fluid is never less than 45°F.
3. During light load periods, artificial heat should be applied directly to the circulating fluid.
A vacuum breaker or air vent should be installed at the high point of the system and an adequately sized drain should be installed At the low point to permit emergency drainage of the coil.
5. All outdoor water lines and the spray pump body should be traced with heating cable and insulated.
*See appropriate product information for details.
We would like to emphasize again the importance of frequent, regular
visual inspection of the units while in operation during the winter
months. Early detection of a potential cold weather problem can often
result in a simple, inexpensive remedy now, rather than a major repair
and inconvenience later.
Technical Resources
a remote sump installed in a heated space or installing steam/hot
water coils or electric immersion heaters in the
tower basin.
2.All outdoor water lines, including the make-up water line to theunit and drain lines from the unit should be traced with heater
cable and insulated.
3. During operation, frequent visual inspections of the unit mustbe performed regularly to:
a. Insure all operating controls are properly set and functioning
normally.
b. Insure the method of freeze prevention is effective.
c. Discover any icing conditions before they develop to the point
where the unit is damaged or system performance is impaired.
4. A regular preventive maintenance program must be established
and carried out despite adverse weather conditions. Items
covered should include:
a. Regular lubrication of moving parts.
b. Regular checking of the make-up value and cleaning of
strainers to prevent high water levels in basin.
c. Regular checking and cleaning of hot water distribution system
to assure uniform flow over unit.
Coil Protection for Closed Circuit
Cooling Towers
1. Charge the coil with ethylene glycol to prevent the system fluid from freezing. The percentage of ethylene glycol should be determined based upon the conditions in your area.
2. If no ethylene glycol is used, adequate* flow through the coil must be maintained so that the temperature of the circulating fluid is never less than 45°F.
3. During light load periods, artificial heat should be applied directly to the circulating fluid.
A vacuum breaker or air vent should be installed at the high point of the system and an adequately sized drain should be installed At the low point to permit emergency drainage of the coil.
5. All outdoor water lines and the spray pump body should be traced with heating cable and insulated.
*See appropriate product information for details.
We would like to emphasize again the importance of frequent, regular
visual inspection of the units while in operation during the winter
months. Early detection of a potential cold weather problem can often
result in a simple, inexpensive remedy now, rather than a major repair
and inconvenience later.
Technical Resources
MAINTENANCE PHOTOS:
http://picasaweb.google.com/sosleny305/MaintenanceLaGorce#
OTHERS LINKS:
EMPLOYEES/JOB DESCRIPTION:http://equiposlagorce.blogspot.com/2008/09/equipos-la-gorce.html
IRRIGATION SYSTEM: http://equiposlagorce.blogspot.com/2008/09/blog-post.html
RULES AND REGULATIONS: http://equiposlagorce.blogspot.com/2008/09/blog-post_08.html
SECURITY ROBER: http://equiposlagorce.blogspot.com/2008/09/security-rover-job-description.html
APARTMENTS:http://lagorceapartments.blogspot.com/
TRANSLATER: http://babelfish.yahoo.com/
SURVEYS: https://www.opinionoutpost.com/membersurveys.php
No comments:
Post a Comment